serviços
O principal objetivo de toda empresa é garantir a satisfação de seu maior patrimônio, o seu cliente, entretanto para que esta satisfação seja alcançada é de fundamental importância que seus produtos e serviços tenham qualidade e sejam frutos de processos eficientes e eficazes.
Quando se fala de qualidade de produtos, logo pensamos em tempo de vida útil e precisão no funcionamento, mas como podemos prolongar a vida de nossos instrumentos de medição e manter a confiabilidade em nossos processos em relação aos resultados obtidos?
A Instrutemp oferece três tipos de serviço para garantir a melhor funcionalidade do seu equipamento:
How do I ship my equipment?
1 - Download the form
Download the "Equipment Submission Form" HERE and fill in the requested data.
2 - Fill in the form correctly
Remittance Invoice for Repair (Operation Code – CFOP 5915 for customers in the State of São Paulo and 6915 for outside the State of SP).
ATTENTION: We do not receive the equipment without the form and without Invoice
3 - Send to address
Unit 1 - Logistics and laboratory
Rua Fernandes Vieira, 156 – Belenzinho - São Paulo – SP CEP:03059-023
Opening hours: Monday to Friday from 08:00h to 12:00h and from 13:00h to 17:30h;
technical assistance and maintenance
Instrutemp's technical assistance offers corrective and preventive maintenance services for all measuring instruments, warranty coverage*, in addition to providing original parts and accessories from partner brands.
We have our own laboratory, we have a team of technicians in metrology and mechatronics, all trained and with extensive experience in maintenance, repair and adjustments of the most diverse equipment and brands.
*Warranty coverage is subject to evaluation and does not apply to misuse.
I want to send my equipment
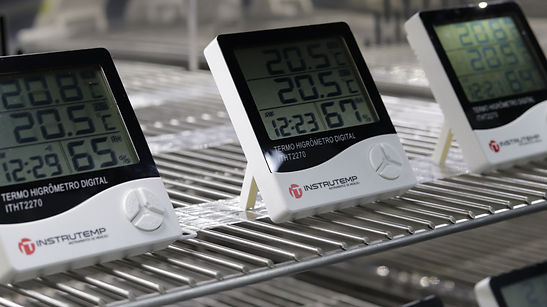
WE OFFER RBC TRACKED CALIBRATION SERVICE MEETING THE REQUIREMENTS OF ABNT NBR ISO/IEC 17025
With trained professionals, modern standards and its own laboratory, Instrutemp offers the best calibration services
Our services have registered reliability RBC Calibration Certificate meeting the requirements according to ABNT NBR ISO/IEC 17025 Standard. Calibration is expressed through a label and certificate, indicating an associated measurement uncertainty, following the procedures guided by the General Coordination of Accreditation - CGCRE for different instruments, guaranteeing the excellence of our services.
SCOPE OF CALIBRATIONS
RBC Tracked Calibration forelectric line
-
multimeter
-
Pliers ammeter
-
function generator
-
Process Calibrator
-
Oscilloscope (Voltage and Current only)
-
resistive decade
-
megohmeter
-
microohmmeter
-
milliohmmeter
-
AC/DC hypot
-
pile thermometer
-
thermometer pliers
-
TTR Turns Ratio Meter
-
Capacitor
-
frequency meter
RBC Tracked Calibration forlaboratory line
-
Thermo hygrometer
-
thermocouple
-
Globe thermometer
-
Process calibrator with temperature function
-
Temperature and humidity datalogger
-
Freezer Thermometer
-
Infrared thermometer
-
thermal imager
-
Analog thermometer
-
psychrometer
-
Dew Point Meter (Dew Point)
-
Temperature and Humidity Transmitter (4-20mA)
-
Water Activity Meter
RBC Tracked Calibration forWork Safety Line
acoustics
-
decibel meter
-
Dosimeter
-
Acoustic Calibrator
brightness
-
lux meter
Speed
-
Rotary Blade Anemometer
-
Hot Wire Anemometer
-
PITOT tube
RBC Tracked Calibration forphysical chemistry line(Analytics, Gases and Time)
analytics
-
PH meter
-
Conductivity Meter
-
Refractometer (BRIX only)
gases
Gas and Combustion Analyzer
-
CO / CO2 / NO / SO2 / O2
4 Gas Detectors
-
CO / H2S / LEL / O2
5 Gas Detectors
-
CO / H2S / LEL / O2 / PID
-
CO / H2S / LEL / O2 / VOC
-
CO / H2S / LEL / O2 / NH3
-
CO / H2S / LEL / O2 / PH3
SINGLE and FIXED detectors
-
CO / H2S / LEL / O2 / PID / VOC / PH3 / CL2
Time
-
stopwatch
RBC Tracked Calibration forMechanics Line
Pressure
-
Differential Pressure Gauge
-
Analog Pressure Gauge (UNDER REQUEST)
-
Barometer
-
Pressure Transmitter (UNDER REQUEST)
-
Vacuumometer (UNDER REQUEST)
Rotation
-
Tachometer (Contact and Optical)
Force
-
Dynamometer (Up to 20Kg)
-
Metal Alloy Durometer
Dimensional
-
Analog / Digital Caliper (Up to 200mm)
-
Analog / Digital Micrometer (External Up to 100mm)
-
Ultrasonic Ink Layer Thickness Gauge
-
Ultrasonic Sheet Thickness Gauge
Vibration
-
Vibration Meter (By mechanical displacement)
downloading patterns
All our equipment comes with the technical report/certificate of calibration and a copy of the REFERENCE STANDARD, available for download below. To identify your standard, just locate the code used in your last calibration and compare it with your equipment. If it is not available, check the date of the last calibration to identify if your calibration has expired, as your equipment will probably need a new calibration.

technical support
We offer technical support for every line of instruments sold by Instrutemp. Our highly qualified technical team is ready to answer technical questions about applications and equipment.